Is your project demanding a custom rubber part? Here's what you need to know."
- Rodney Dsouza
- Mar 21
- 3 min read
From design headaches to production hurdles, we will help to break down the rubber product journey.
We all know that finding a reliable partner for custom rubber manufacturing can be challenging. At Stanro Rubber Engineers we simplify the process with our collaborative approach and technical expertise. We come in when off-the-shelf rubber components fall short and you need a custom solution.
Here’s how it works.
Stage 1: Concept and Design

Understanding the Client's Needs:
We begin by thoroughly understanding your application requirements through in-depth discussions. We can meet over a call and utilize CAD models and online collaboration tools, or even in person to understand the application better.
Design Collaboration:
We collaborate with your engineers to advise during design and proactively identify potential design as well as manufacturing challenges and provide solutions to prevent costly rework later in the process.
Material Selection:
Choosing the right rubber material is paramount to achieving optimal performance and longevity for your product. Using an inappropriate material can lead to premature failure, costly replacements, and compromised product integrity. With a wide range of rubber materials available, each with unique properties, selecting the ideal compound requires specialized knowledge and experience. We can help you analyze your application requirements and recommend the most suitable material to meet your specific needs.
Stage 2: Prototyping and Testing
Prototyping is your insurance against costly mistakes. It allows us to identify and address potential design flaws before investing in expensive production tooling.
A prototype allows us to test the form, fit, and function of your rubber component in real-world conditions. It allows for iterative design, enabling us to refine the design and optimize performance based on testing results thereby having a physical proof of concept.
Stage 3: Manufacturing and Production

Tooling and Mould Design:
We need to understand that every rubber compound and product design requires a unique mould design, tailored to its specific characteristics.
The mould has to be such that even during high-volume production, the repeatability and accuracy of the parts is not affected. We use high-quality materials and construction techniques to ensure our molds are durable and long-lasting.
Production Process:
Any rubber production process needs to be designed for optimal efficiency, ensuring timely delivery of your custom rubber components. We have a streamlined workflow, from raw material handling to final inspection, ensuring smooth and efficient production.
We have the ability to handle a variety of rubber compounds and can easily manage a wide range of production volumes, from small prototypes to large-scale production runs. Roughly, a step wise process will look as follows:
a. Raw Material Handling
b. Compounding and Mixing
c. Molding and Curing
d. Finishing and Trimming
e. Inspection and Quality Control
f. Packaging and Shipping

Quality Control:
We understand that the performance and reliability of your products depend on the quality of our rubber components. A quality component ensures reduced risk of product failure and rework. That's why we take quality control seriously.
We are an ISO 9001 certified company and our team has extensive experience in rubber manufacturing and its quality assurance. Raw material Inspection, In-process Inspection and Final Inspection along with validation ensure that products will meet or exceed your expectations, every time.
Stage 4: Completion and Delivery
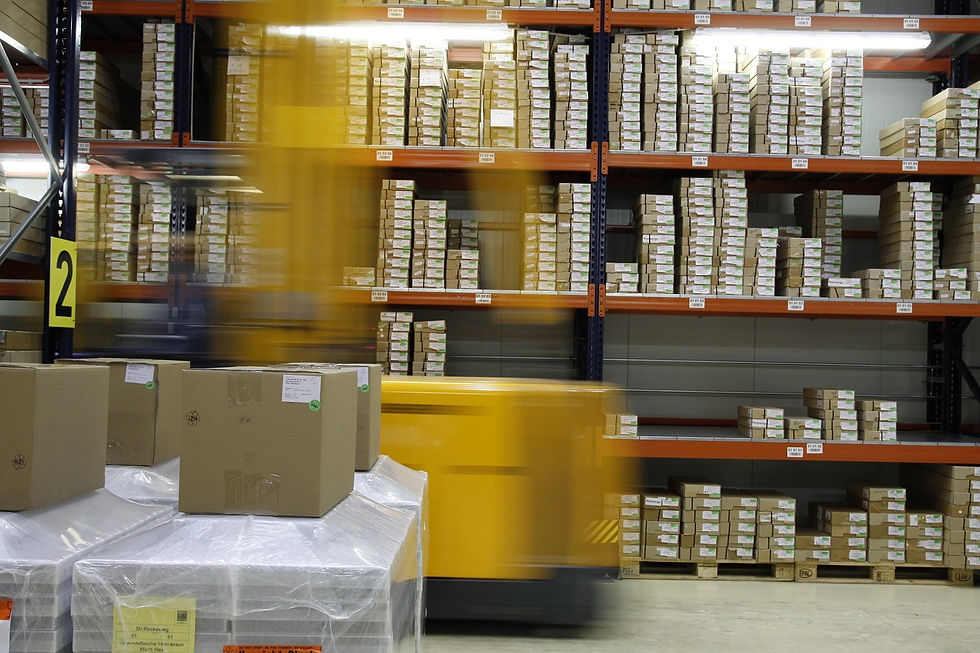
Finishing and Packing:
We employ precise trimming and deflashing techniques to remove excess material and achieve the desired product dimensions. These parts are thoroughly cleaned and checked.
For certain FKM or Silicone applications, we can perform post curing cycles to further enhance the properties of the finished product. We provide clear and accurate labeling to ensure proper identification and traceability of your products. We can even include custom labels with your company logo, product information, or any other required details.
We can handle domestic and international shipments, providing you with flexible shipping options.
Customer Support:
Even after the material has been received you, we are available to address any questions or concerns you may have after receiving your order. We understand that every customer is unique, and we tailor our support to meet your specific needs.
We factor your feedback and try to improve our products and services to meet your personalized requirements.
In case of any queries or ambiguities regarding our supplied parts or for new developments, all you have to do is reach out to us, and we will be more than happy to help out!
Comments